1. Principle
A comprehensive logging equipment equipped according to the standard needs to measure pump pressure, casing pressure, WOB, hook load, rotary table torque and other parameters. In addition to Hall electric torque sensor used by electric drilling machine, four sets of pressure sensors are generally required, including 0-5mpa pressure sensor for measuring drilling hook load and rotary table torque of non electric drilling machine, and 0-40MPa pressure sensor for measuring mud pump pressure And well casing annulus pressure.
IML-P is a kind of dry-type ceramic piezoresistive sensor, which is made of imported ceramic materials and refined by special process from Germany. Ceramic is a kind of material with high elasticity, corrosion resistance, wear resistance, impact resistance and vibration resistance. The thermal stability and thick film resistance of ceramics can make its working temperature range as high as – 40 ℃ ~ + 120 ℃, and it has high accuracy and stability. The electrical insulation degree is more than 2KV, the output signal is strong, and the long-term stability is good. There is a trend to replace other types of sensors in Europe and America.
The output of the sensor adopts 4-20mA two-wire industrial standard. Its shell adopts corrosion-resistant stainless steel and German Hirschmann connector. The protection grade can reach 1p65. Besides oil field, it is widely used in many industries, such as industrial control, mining, food processing, automobile, electronics, medical treatment, etc.
2. Installation and use:
The sensor can be directly installed on a suitable threaded interface, and the installation position has no effect on the measurement. In order to meet the CE standard, shielded cable must be used, and the shield layer of the cable must be connected to the shell and the earth.
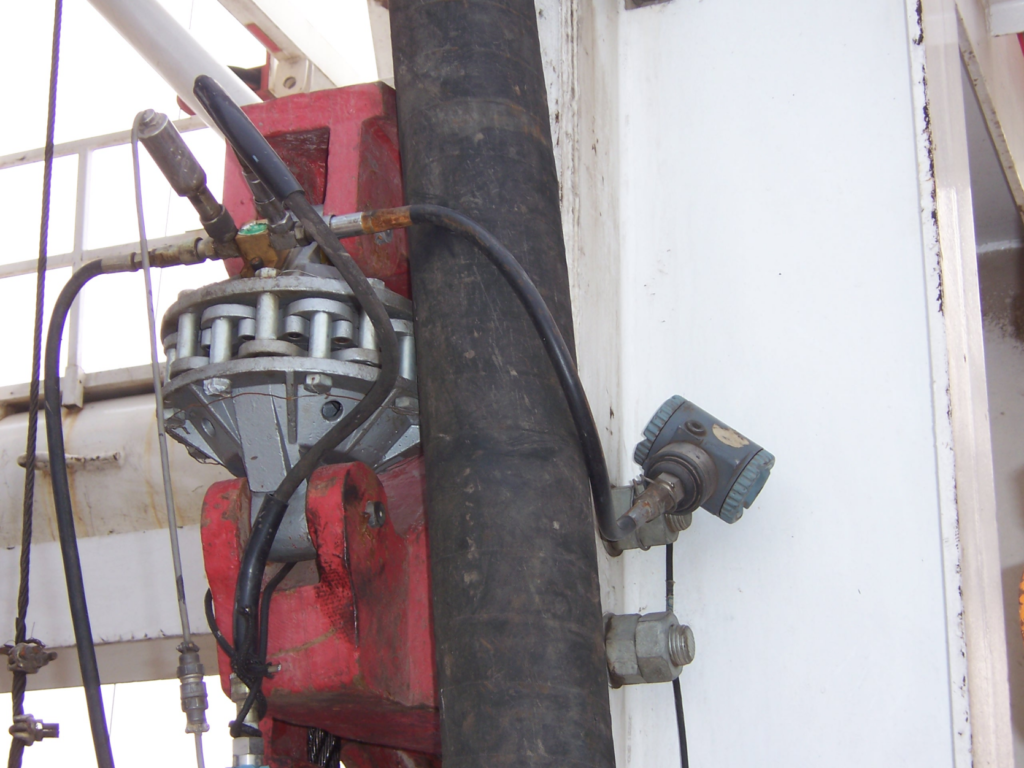
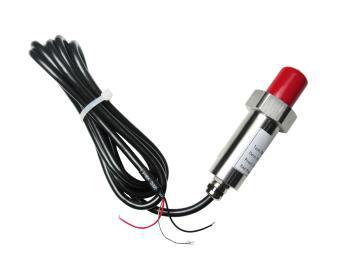
3. General fault judgment
If there is no signal output or output over value during the drilling process of the pressure sensor, first check whether the extension cable is open or through. When the pressure reading is not correct, first check whether the sensor is lack of hydraulic oil or whether there is air bubble in the oil circuit. In case of oil shortage, the manual pump shall be used for oil filling, and if there are bubbles, the bubbles shall be discharged.
If it is suspected that the pressure sensor is faulty, the connection between the sensor and the piston pressure gauge can be removed. According to the engineering range of the sensor, when the input voltage is zero and the full range, the signal current should be about 4 and 20 mA respectively, otherwise the sensor is faulty and sent back to the company for maintenance.
There are two potentiometers in the sensor that can be used to adjust the output zero point and full range value of the sensor. Unplug the Hirschmann connector and the rear cover of the sensor, and you can see that 504 × is the zero point adjustment, and the other one is the full range adjustment. Connect the current and standard pressure source, adjust 504 × potentiometer when the pressure is zero, and the output of the sensor is 4mA, and then adjust the pressure source to the full range pressure Adjust the other potentiometer to make the sensor output 20mA. Repeat the adjustment for two or three times.
For oilfield users, the general required elegance is: 1.6Mpa, 6Mpa, 20MPa, 40MPa. It can be supplied for any other range within the range of 0-50mpa.